Material
Characterisation
Accurate analysis predictions are reliant on precise material properties. This is particularly relevant for the complex (orthotropic) properties of composite materials, which are a function of fibre, matrix and processing conditions. Characterisation involves physical testing of the material in various ways, and subsequent calculation of properties based upon the raw test results. Thus a ‘material card’ is created for use in analysis software.
Material Characterisation
CRUSH / FRACTURE TOUGHNESS / DYNAMIC COMPRESSION & SHEAR / FATIGUE / STATIC / ADHESIVE / SANDWICH STRUCTURE/ COMPOSITE MACHINING / CONDITIONING / DIGITAL IMAGE CORRELATION
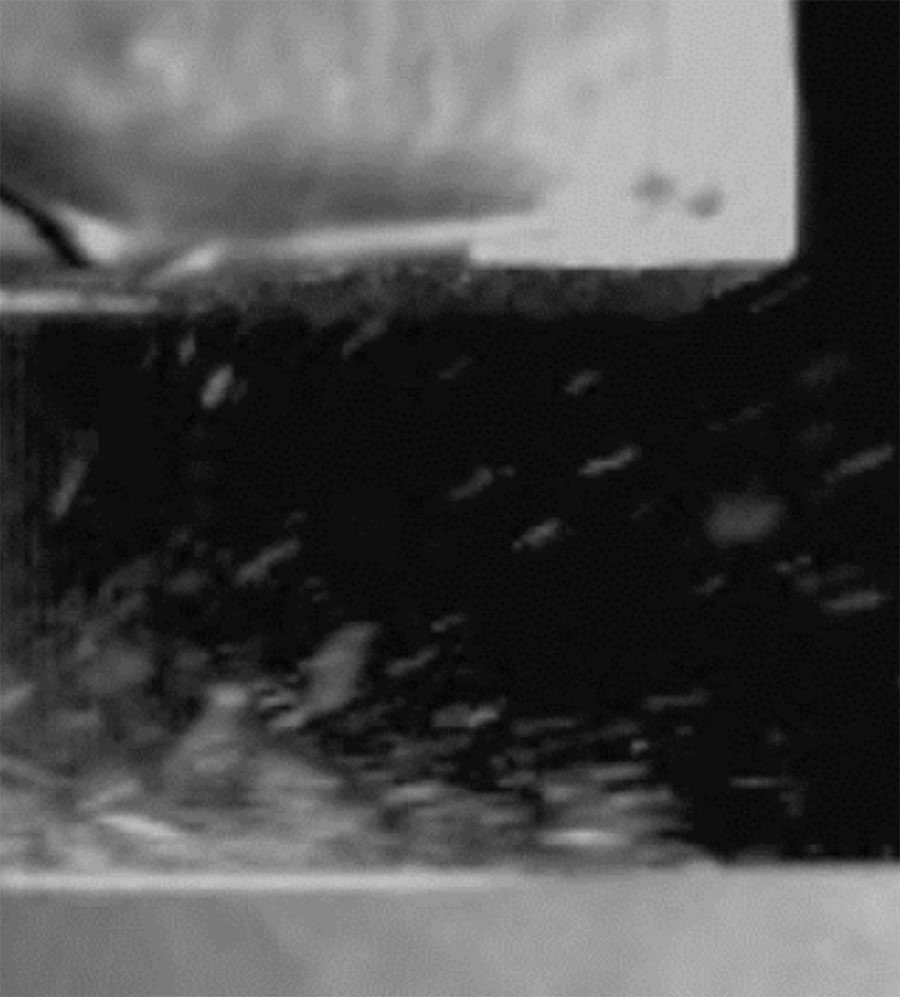
Crush Testing
Composite materials absorb energy most efficiently through material fragmentation. In an impact, they have the ability to absorb significantly more energy per unit weight than metallic structures. Our bespoke drop tower and crush fixtures allow composite crush behaviour to be measured accurately and efficiently. Crush testing also gives insight into material stability and susceptibility to compressive failures. Furthermore, these properties can feed directly in to CZone analyses, allowing crush behaviour to be accurately predicted.
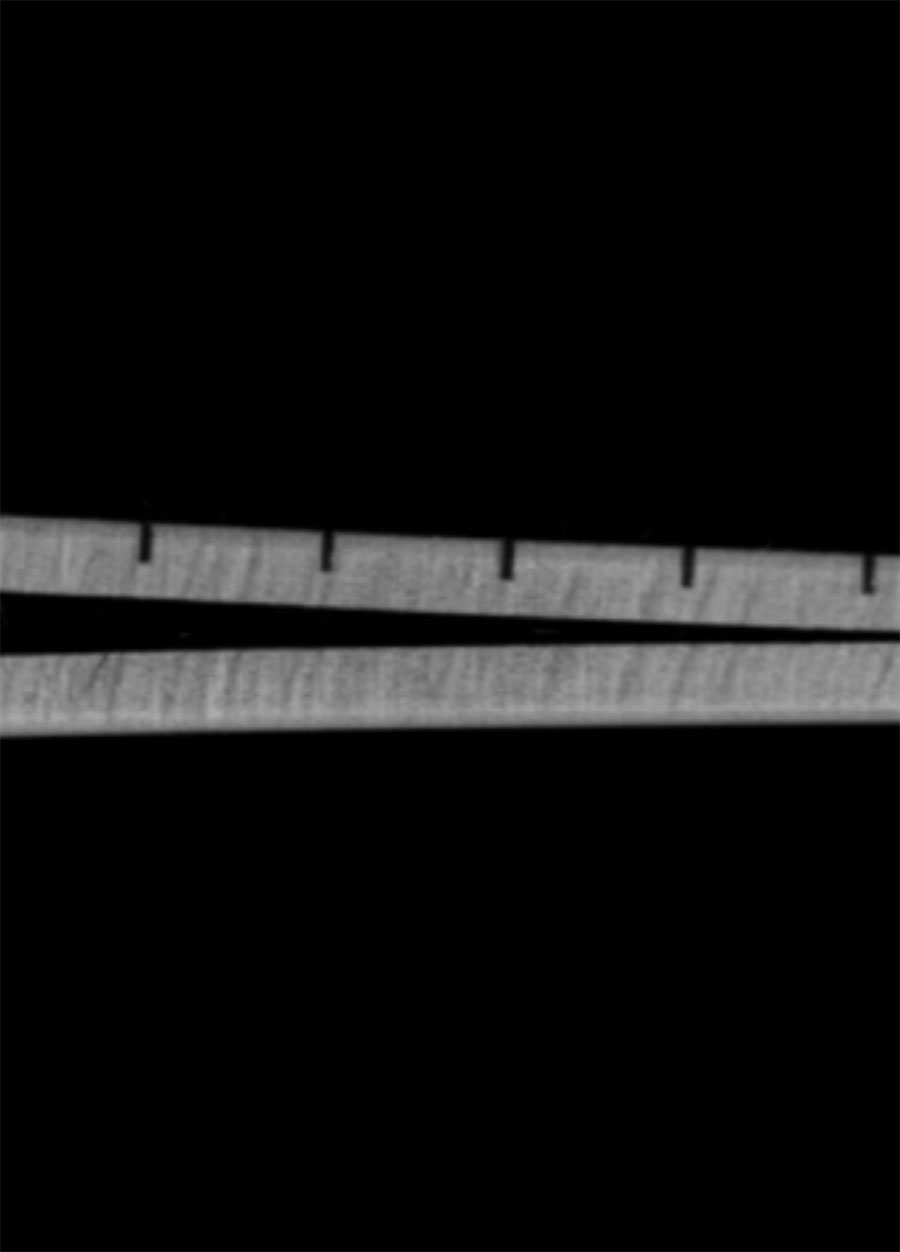
Fracture Toughness Testing
Understanding fracture toughness behaviour is vital for simulating the damage evolution of composite materials. We offer tests for capturing fracture toughness in different modes and can advise on the tests required for specific material cards. We have developed specialist crack detection software for precisely tracking interlaminar and intralaminar crack growth. Tests offered include:
- Modified Compact Tension and Compact Compression for Fracture Energy Release Rate
- Charpy Dynamic Energy Release Rate
- ASTM D7905 End-Notched Flexure
- ASTM D6671 Mixed Mode Bending
- ASTM D5528 Double Cantilever Beam
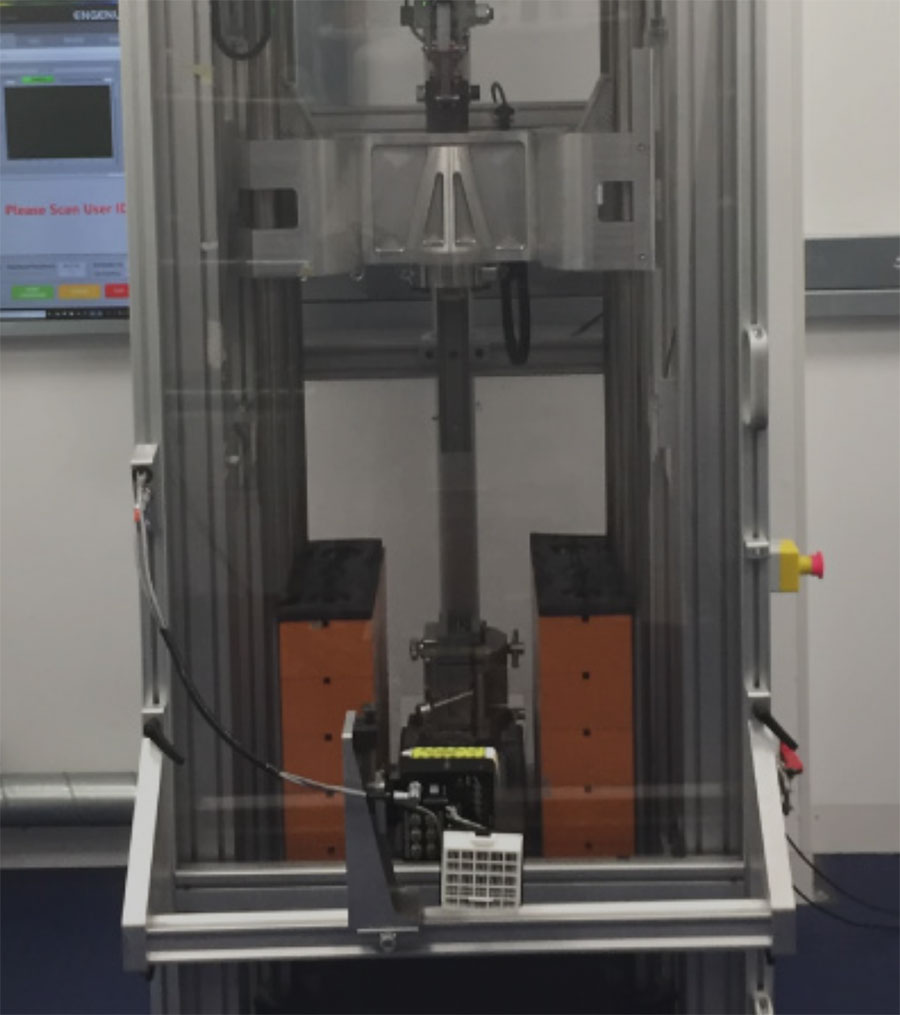
Dynamic Compression and Shear Testing
The compression and shear strengths of composite materials can change with increasing strain rates. In particular, we have witnessed uplifts in strength of between 10% and 50% through our dynamic testing. Our drop tower, high speed cameras and digital image correlation capabilities allow us to measure these characteristics. Rate dependent compression and shear strengths can be incorporated into our Impact Enhanced Ply (IEP) failure material card.
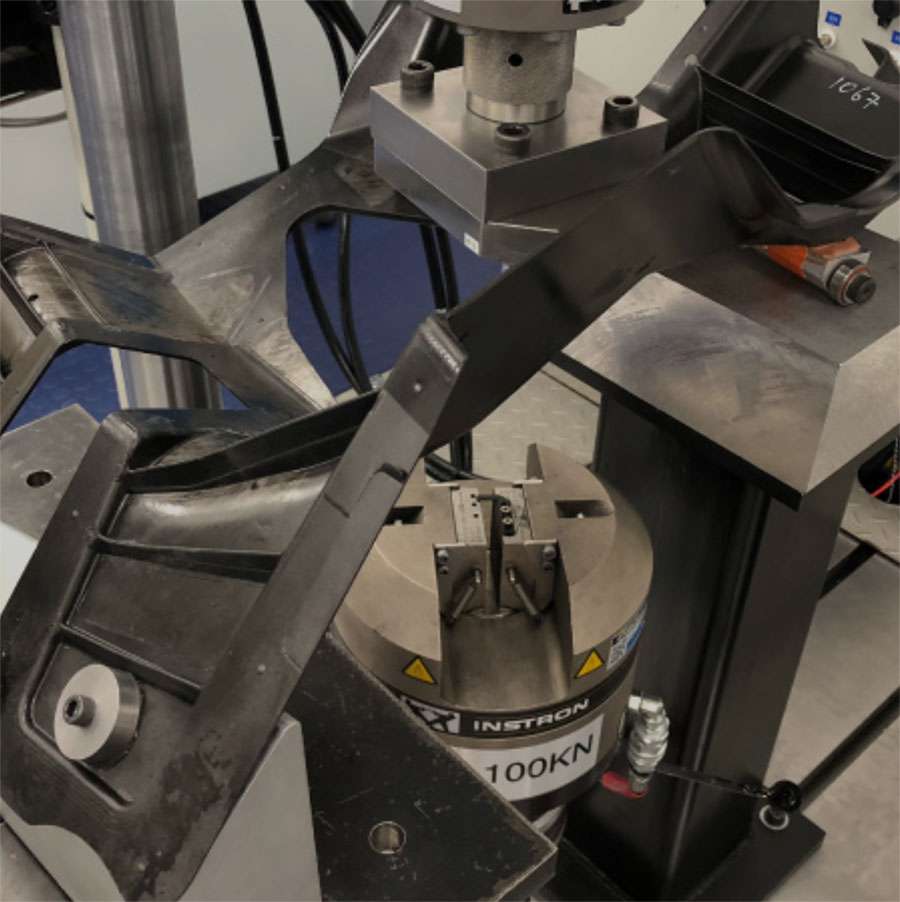
Fatigue Testing
Fatigue behaviour of materials is important when designing for the lifetime of a component. Our test capabilities allow us to measure the fatigue properties of metallic and composite materials at a wide range of amplitudes and frequencies. Our repertoire covers a variety of different coupons types and components. We have, for example, fatigue tested bicycle forks, brake pedals and automotive C-pillar reinforcements.
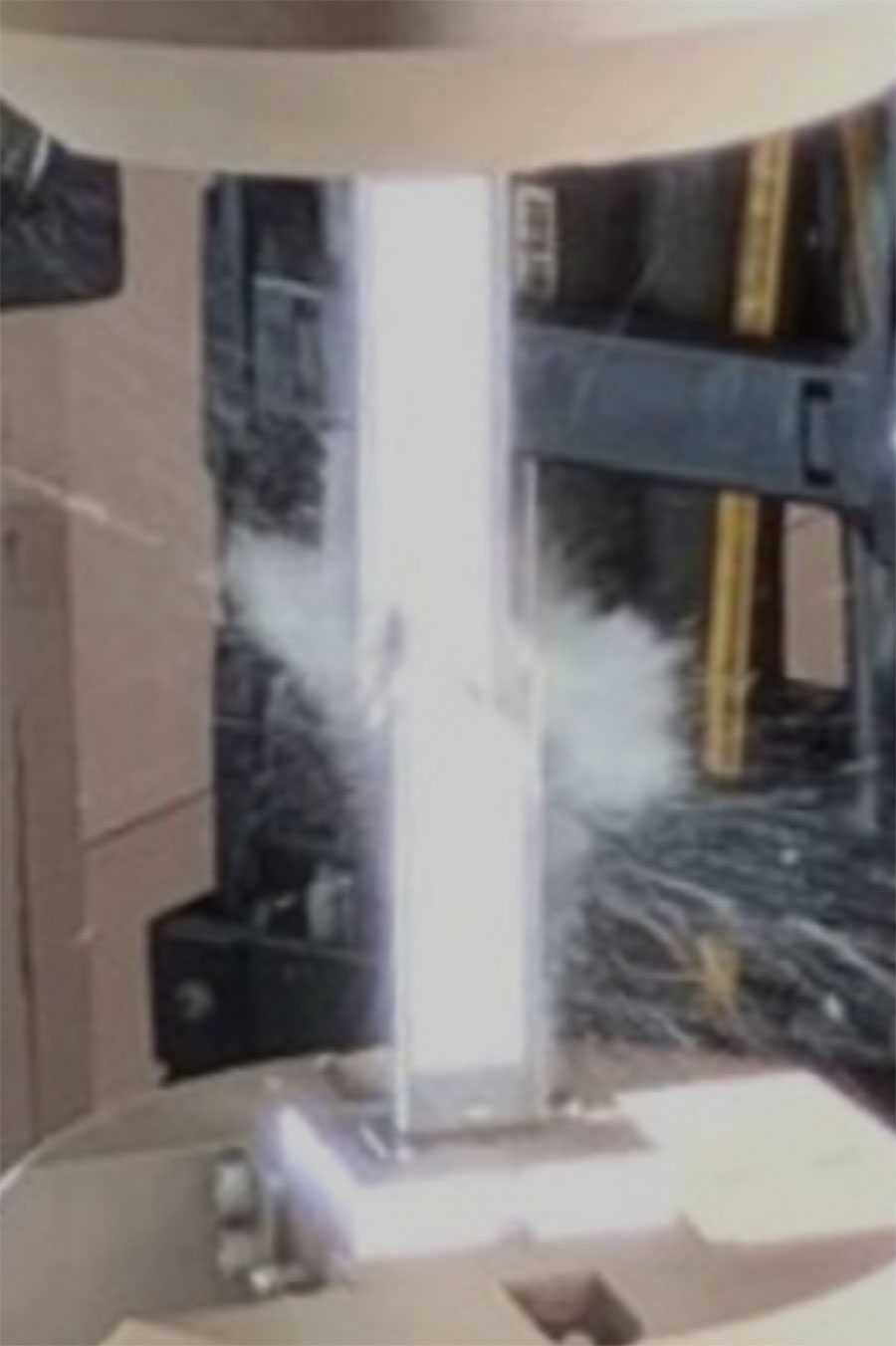
Static Testing
We are equipped to conduct a wide range of tensile, compressive and shear tests at static rates:
– ASTM D3039 Tension
– ASTM D6641 Combined Loading Compression
– ISO 14126 End Loaded Compression
– ASTM D7078 V-Notched Rail Shear
– ASTM D3518 In-Plane Shear
– Cyclic Shear Degradation
– ASTM D2344 Short Beam Strength
– ISO 19927 Double Beam Shear
Front and rear strain measurements are taken for all tension and combined loading compression tests, allowing specimen bending to be measured and modulus to be accurately recorded. The outputs from these tests are useful for comparing materials or forming the basis of analysis material cards. Our own proprietary software saves time and increases repeatability in the processing of results.
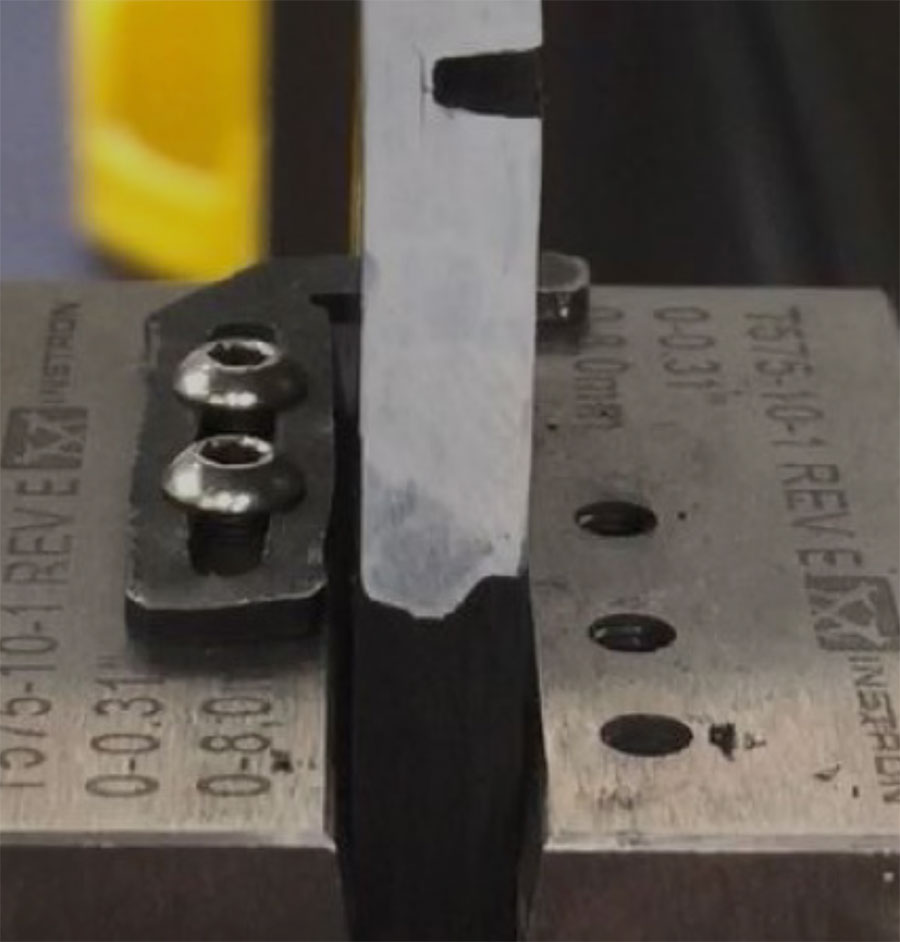
Adhesive Testing
Creating adhesively bonded joints presents one of the greatest challenges in lightweight composite structures, particularly when applied to high volume manufacture. Adhesive performance can be sensitive to bonding technique, adhesive thickness, temperature and moisture, all of which require consideration. Measuring adhesive performance using our lap shear, lap peel and end-notched flexure tests builds confidence in bond performance and allows cohesive connections to be modelled accurately.
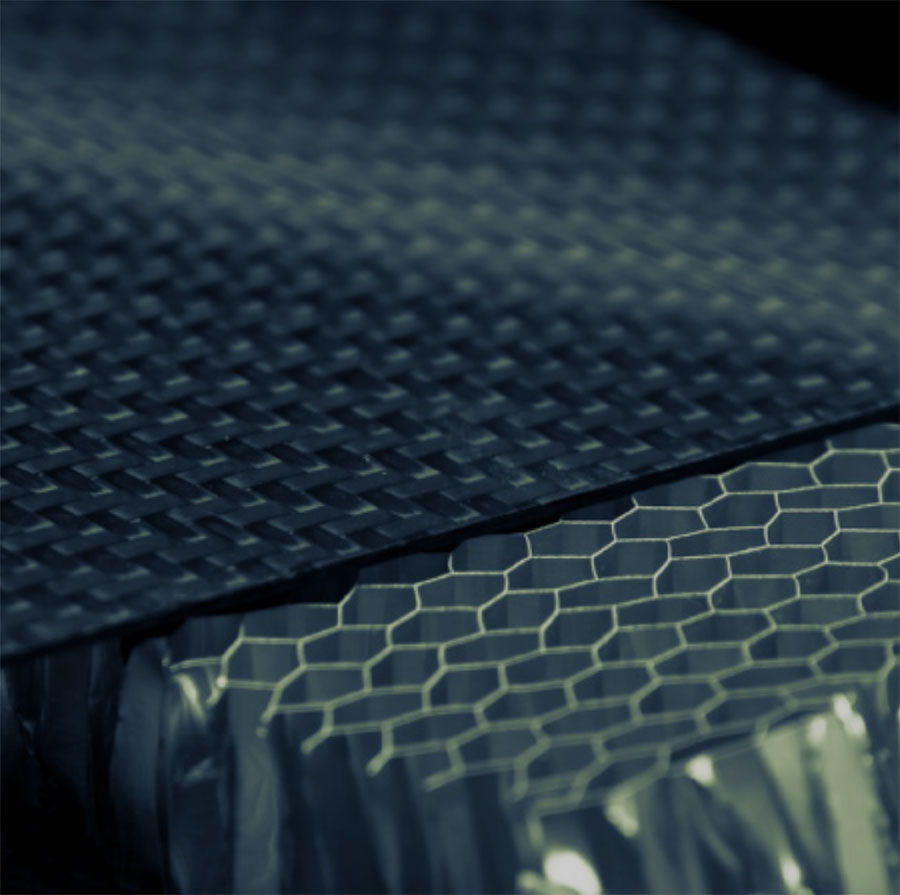
Sandwich Structure Testing
Composite sandwich structures see extensive use where bending stiffness is an important requirement. We can characterise their behaviour with fixturing specifically designed for these structures. The tests we offer are:
– ASTM C273 Sandwich Panel Shear
– ASTM C365 Sandwich Panel Compression
– Facesheet Peel
– Sandwich Panel Crush – Coupons and Sub-Components
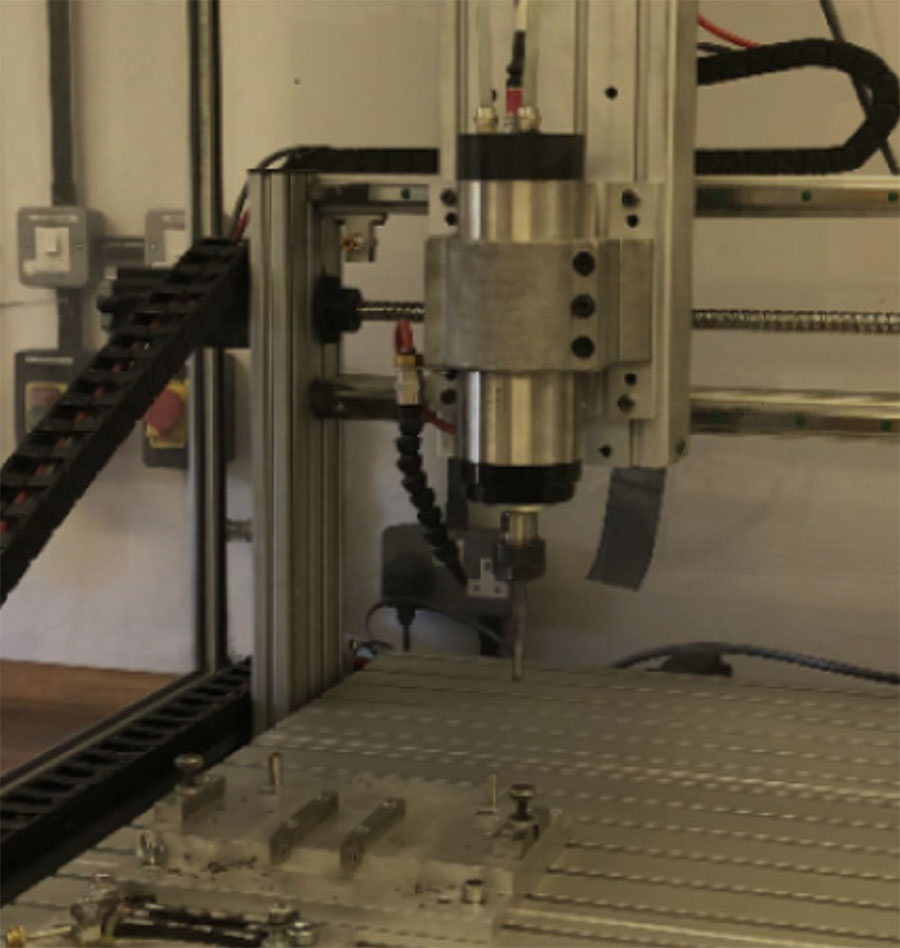
Composite Machining
The quality to which a specimen is machined can vastly affect the outcome of a test. Our machining facility is well equipped and allows us to prepare all of our test specimens in-house. We can produce coupons with complex geometries using our CNC milling machine, diamond saws and notch broaching machine. Our diamond wire saw cutter gives us the capability to machine slots as thin as 0.13 mm. All coupons are produced and quality checked to tight tolerances.
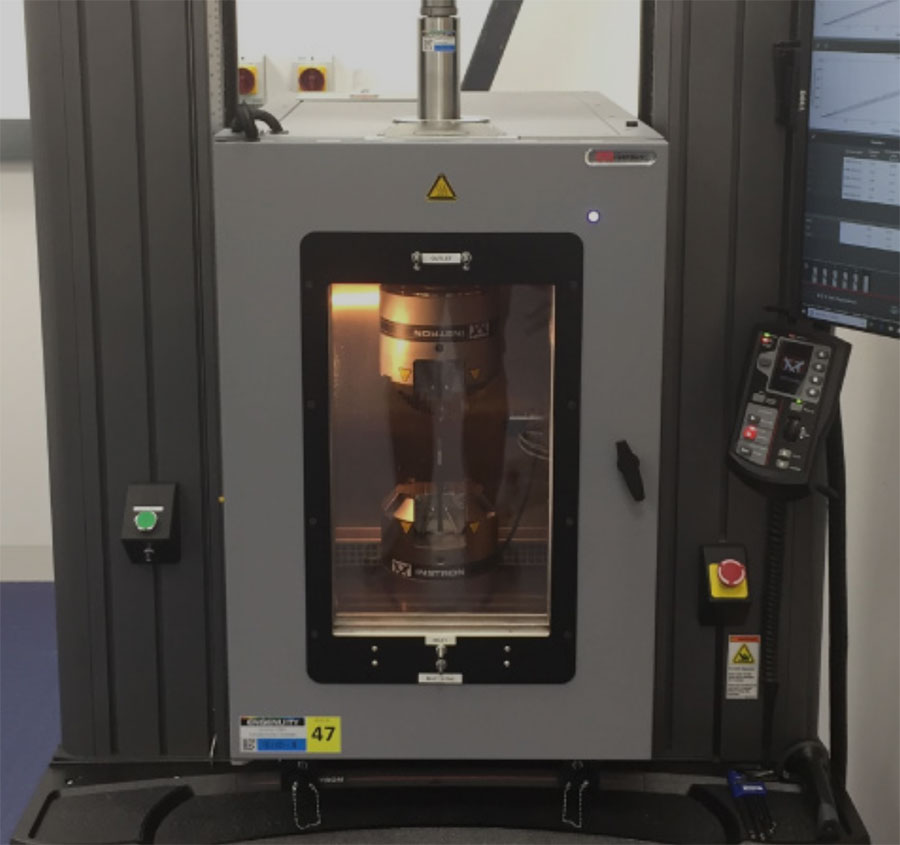
Conditioning
Composite performance can change, sometimes dramatically, with temperature and moisture content. Our environmental chamber enables us to test over a wide range of temperatures, from as cold as -70°C, to as hot as 350°C. Additionally, our precision balances and immersive water bath give us the ability to investigate the effect of moisture content on mechanical properties.
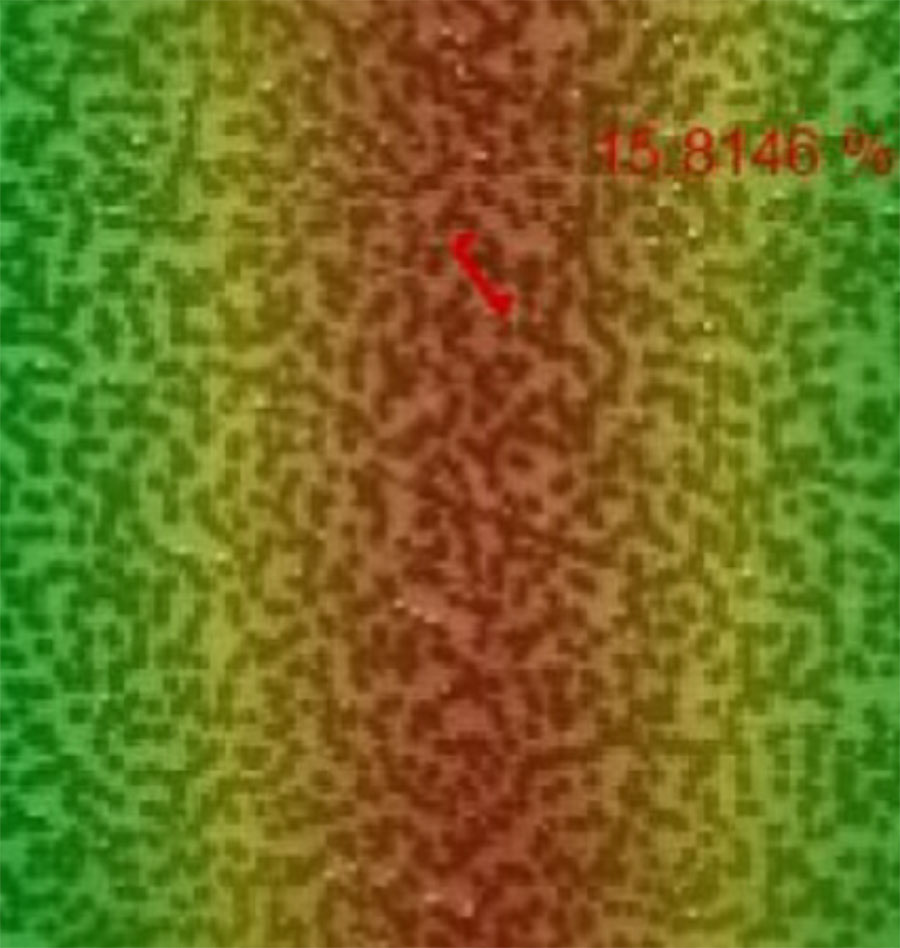
Digital Image Correlation
Using Digital Image Correlation (DIC) for strain measurements holds several advantages over traditional methods. Strain can be captured over a large field, across changing profiles and unlike extensometers, up to the point of failure. All our strain measurements at Engenuity are made with DIC, and our high rate cameras allow us to output precision measurements at up to 900,000 frames per second. Furthermore, our system allows us to produce 3D strain maps of complex geometries.