Engineering
Analysis
Finite Element Analysis is a computational modelling technique which enables prediction of structural performance such as strength, stiffness or energy absorption. The geometry of the component or system can thus be optimised virtually so that it meets all design requirements without recourse to physical testing or prototype phases. The accuracy of any analysis is dependant upon three factors: component geometry, loading definition, and material properties.
Engineering Analysis
STRUCTURAL ANALYSIS / CZONE / FIRMA / CURE DISTORTION / VIBRATION ANALYSIS / FATIGUE ANALYSIS / IMPACT ENHANCED PL
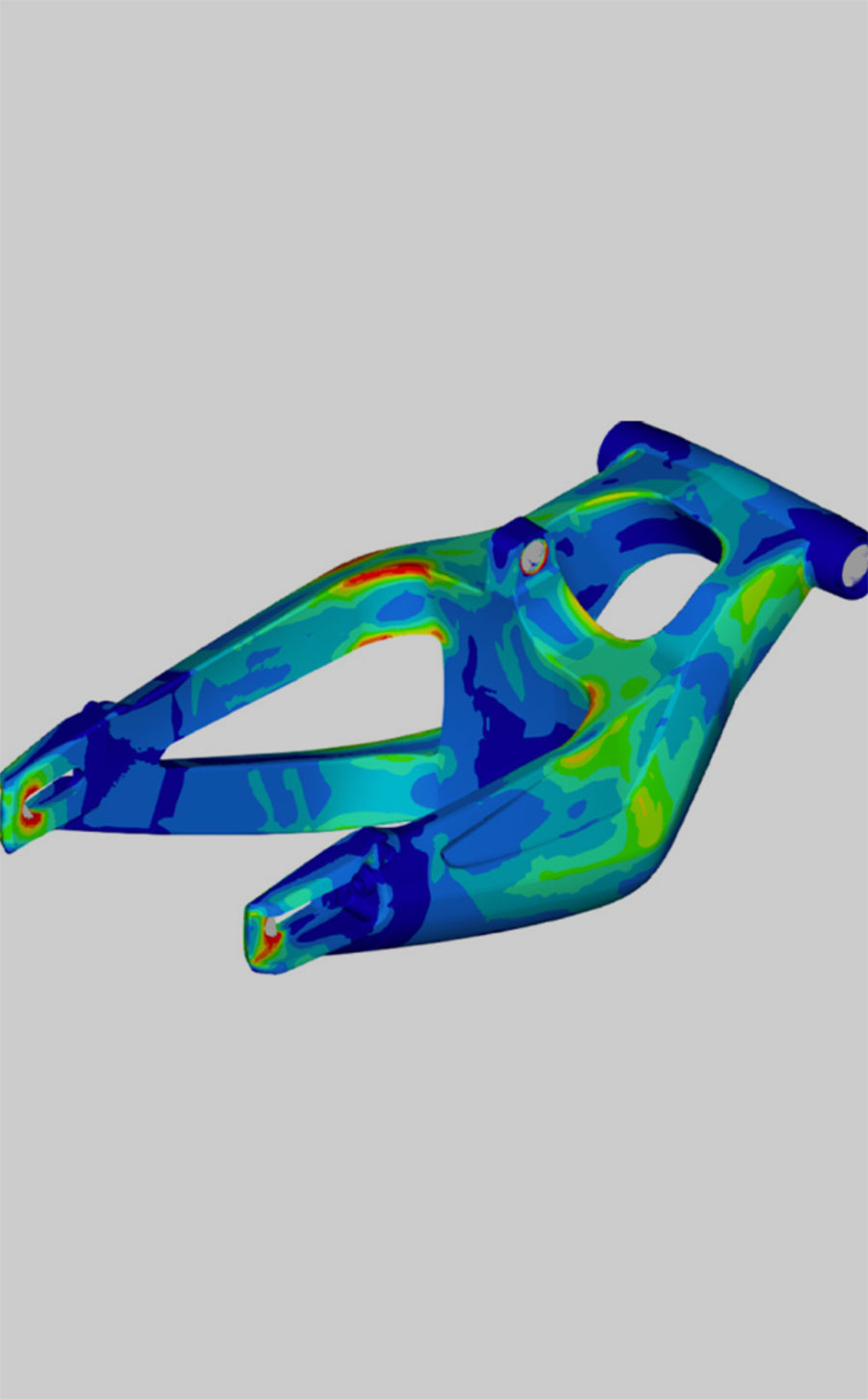
Structural Analysis
Carrying out detailed structural analysis streamlines
development processes, reduces time to market, and predicts part performance before committing to manufacturing. Understanding the stiffness, strength, vibration performance, and weight saving opportunities of parts and structures is vital to developing a competitive product in all industries. Engenuity have vast experience utilising multiple Finite Element Analysis (FEA) solvers and a wide array of structural evaluation techniques:
– Linear static
– Vibration and modal
– Topology and laminate optimisation
– Non-linear implicit
– Full dynamic explicit
We apply these techniques not only to composites, but to all structural materials, from welded steel fabrications to nylon injection mouldings.
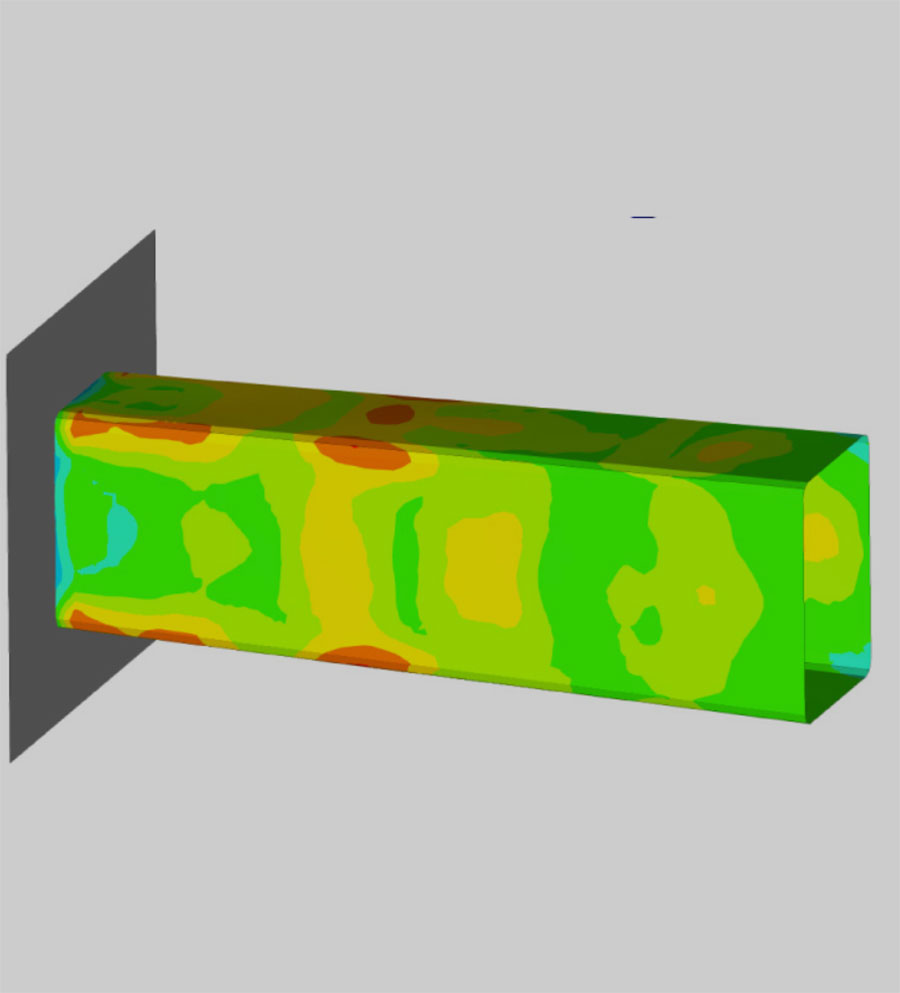
CZone
CZone is Engenuity’s solution to the problem posed by the modelling of composite crush. Measured crush forces from coupon tests are used to define the ply-based crush performance of a material. These properties are applied to models, so when a crushing interface is detected, the loads from a crush front are accurate and element deletion reflects the delamination and fragmentation that occurs. We conduct CZone analyses in house, and the software is commercially available via Simulia as an add-on for Abaqus Explicit.
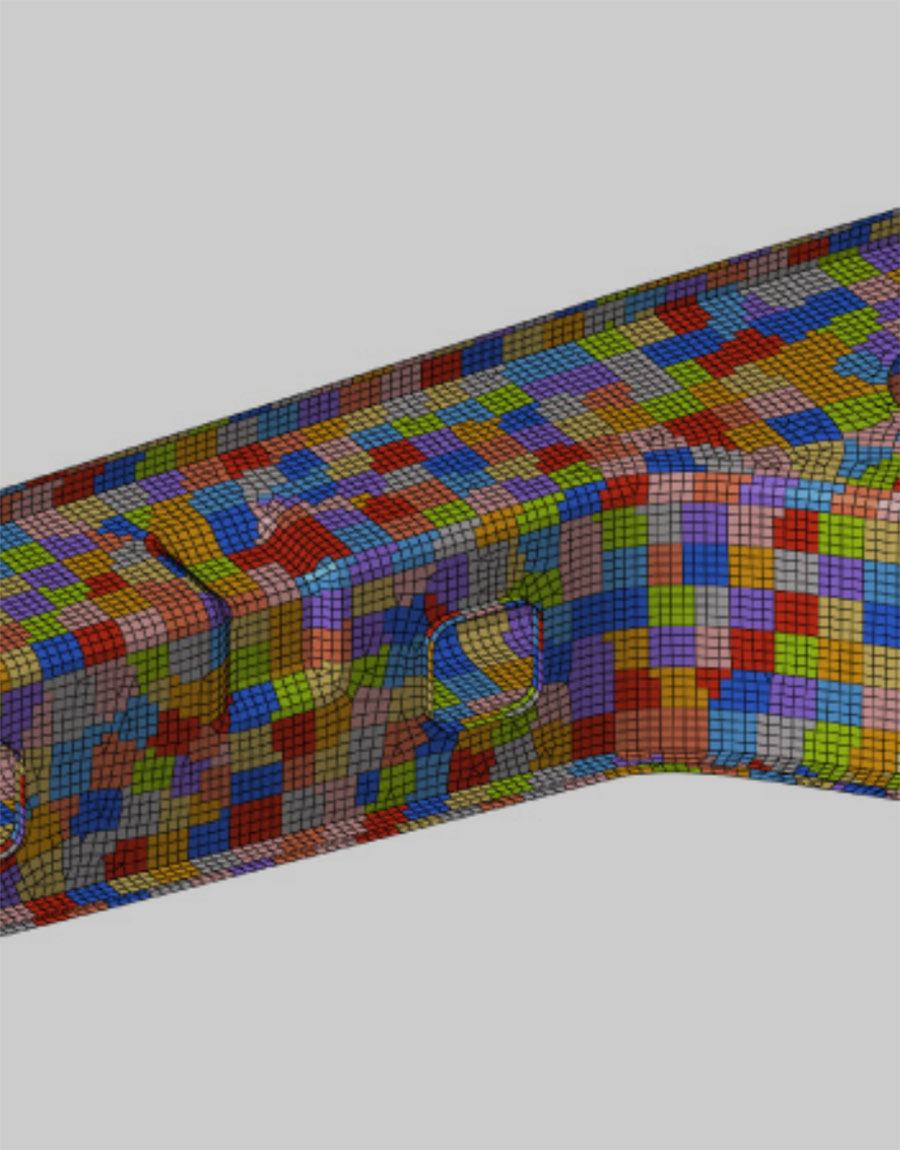
FiRMA
Manufacturing components from Sheet Moulding Compound (SMC) couples low cost constituents (including recycled fibre) with high production volume ability and part reproducibility. Engenuity’s FiRMA (Failure in Random Material Architectures) software allows structural components to be made using chopped and recycled material with confidence, whilst maintaining weight saving potential. FiRMA’s method of material characterisation coupled with stochastic analysis generates a realistic part performance distribution and likelihood of failure. This replaces traditional methods of SMC modelling which are more likely to be pessimistic, returning an overweight product.
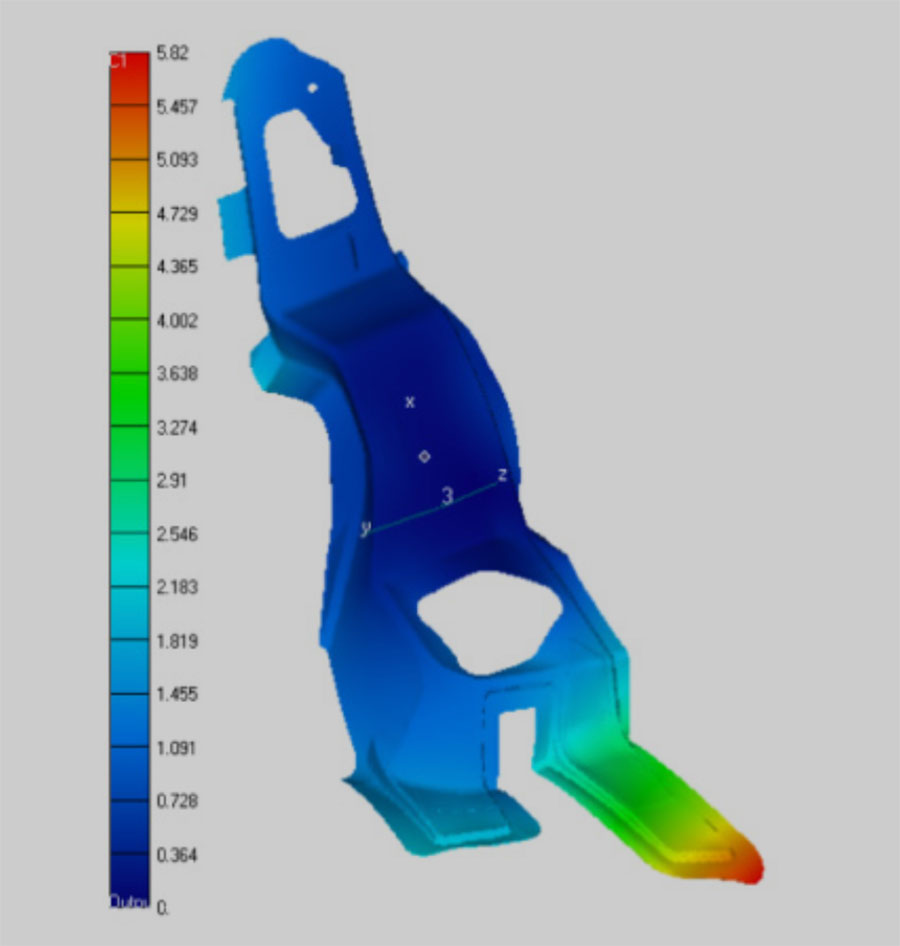
Cure Distortion
During the manufacture of composite components, post cure residual stresses give rise to distorted parts, leading to poor tolerances and assembly issues. Through the testing of materials for relevant thermal and structural properties, we make accurate predictions for post cure residual stresses and therefore can determine how distorted a part will be as it comes out of the mould. This allows us to directly compensate tool geometry CAD, to ensure in-tolerance parts.
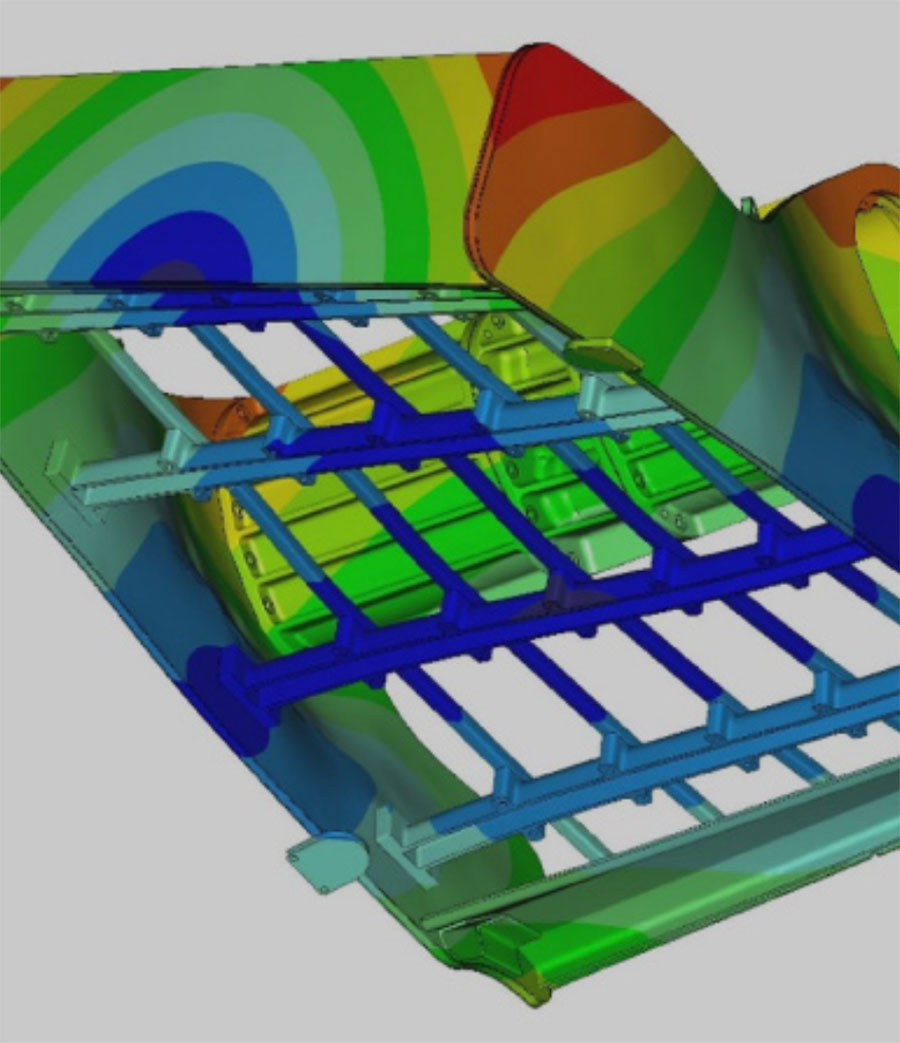
Vibration Analysis
Avoiding resonant modes in many structural assemblies is vital, as running machinery at a matching or near frequency can result in harsh vibration damage and fatigue failure of components. Vibration analysis is invaluable in the design of any engineering component or assembly that experiences an oscillating input spectrum. We can predict modal frequencies before components are committed to manufacturing and hence engineer the structure to avoid them – leading to cost and time savings. Our fully detailed analysis models capture all aspects of the structure and design details that contribute to the modal performance.
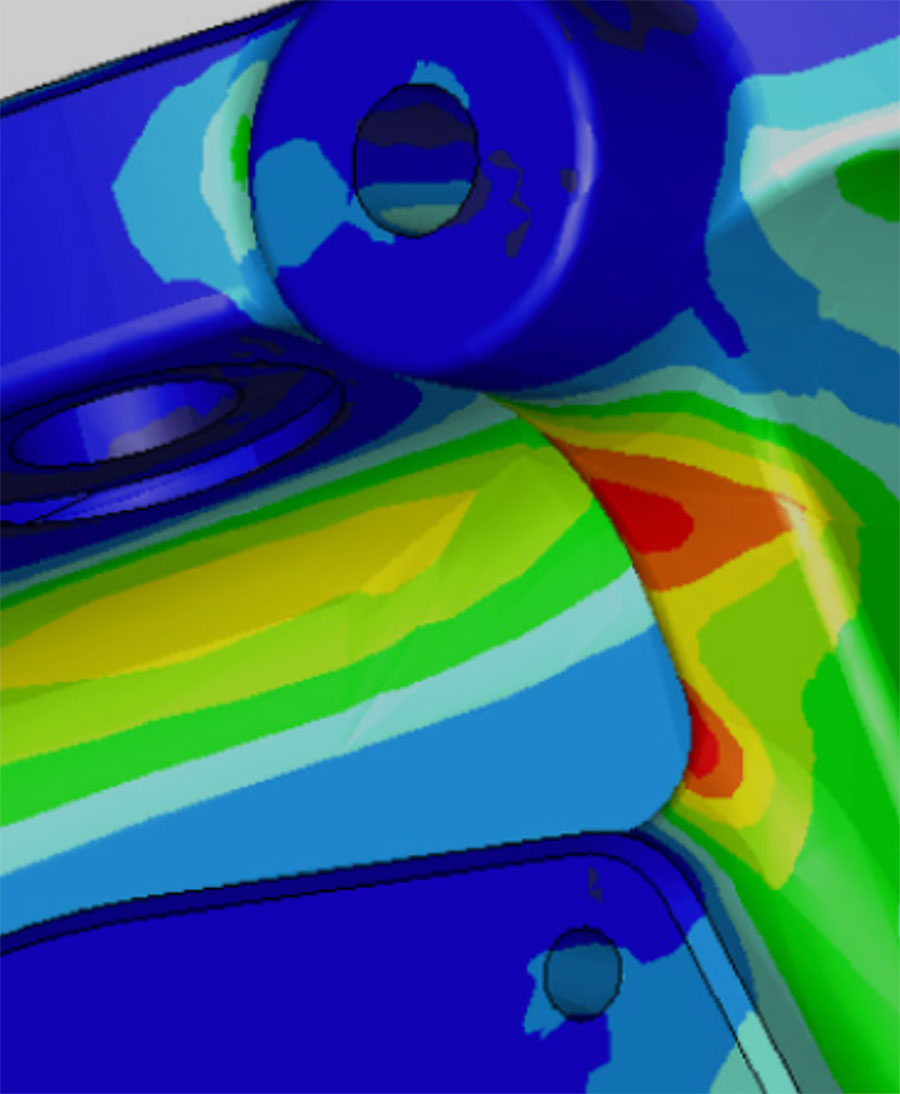
Fatigue Analysis
Understanding the fatigue life of a design can be the difference between a robust, reliable and highly valued product and a costly recall or excessive development budget. Engenuity can calculate and develop the fatigue life of your structure, be it a single material with complex and detailed features, or a multi grade welded fabrication. Loading cycles (derived by data acquisition testing if required), are applied to detailed finite element models which include precise material models. This results in an in depth understanding of how a design will perform, with clear indications of potential fatigue hotspots and recommendations of how to avoid premature failures.
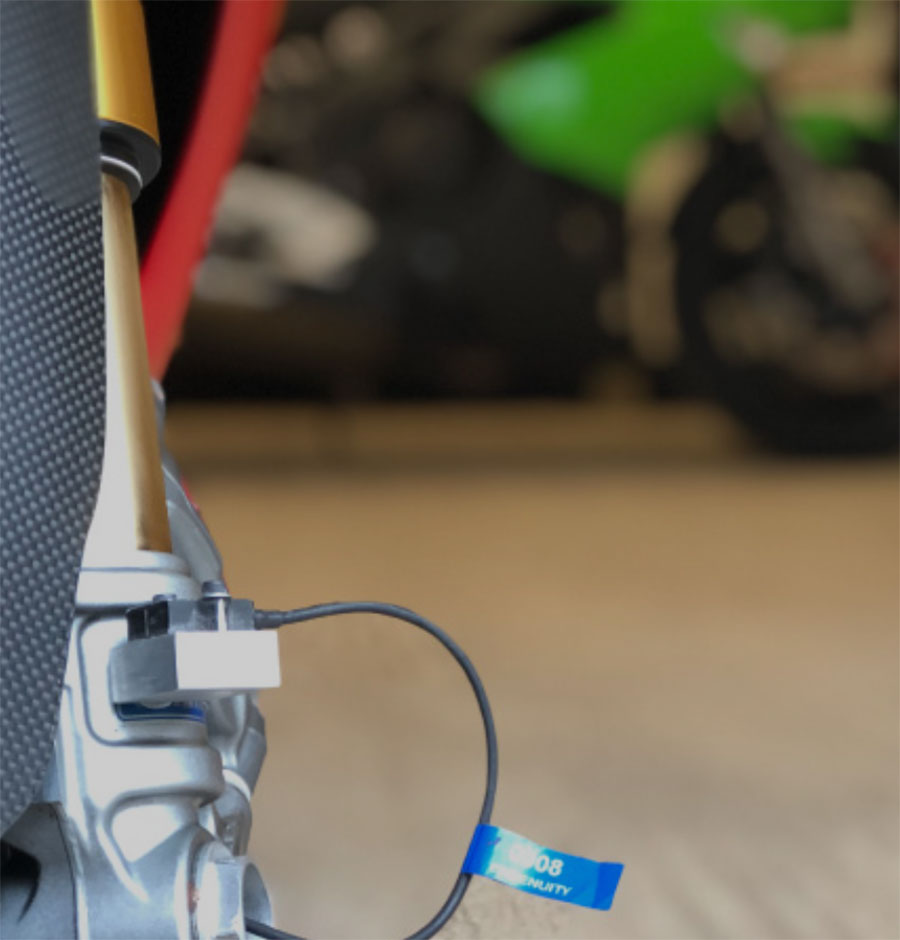
Data Acquisition
For structural analysis it is often critical to establish a correct loading spectrum. Our compact adaptable acquisition system records data in-situ – whether braking loads on a motorcycle or vibration input to heavy machinery. We position sensors (accelerometers, strain gauges, potentiometers) at carefully considered locations. This allows us to identify the loading conditions experienced by structures in real life, enabling the exact criteria and fatigue loadings to be defined for subsequent design development.
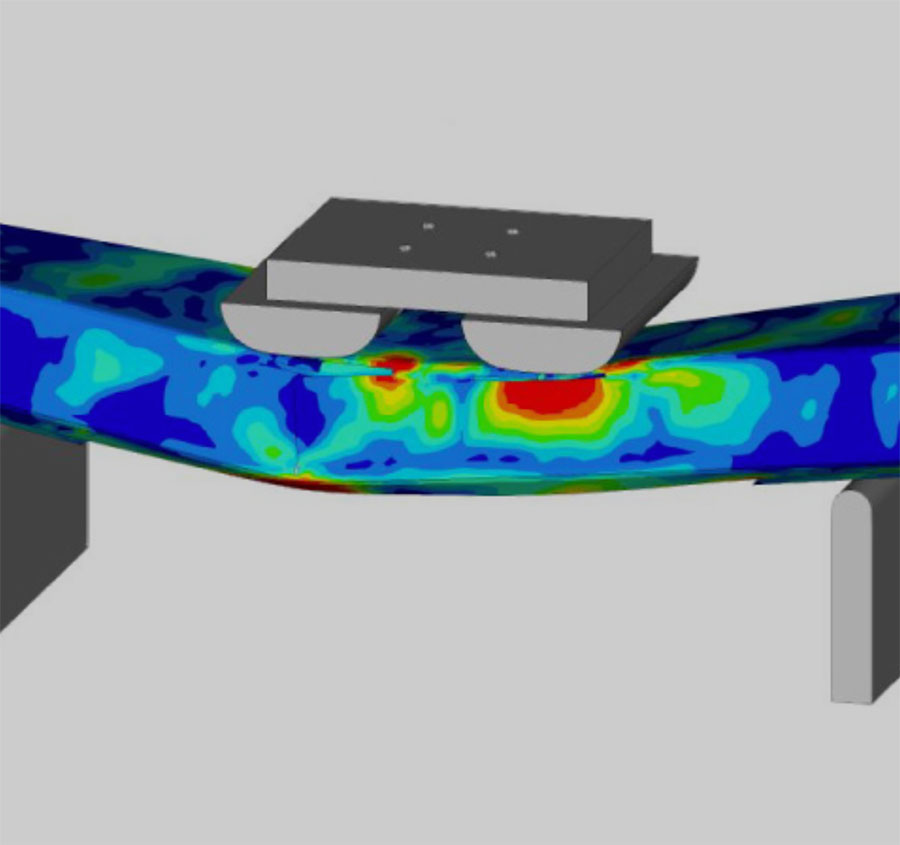
Impact Enhanced PLY
Engenuity’s Impact Enhanced Ply (IEP) material card is one of the most comprehensive ways of defining the properties of a composite in analysis simulations. The card allows the user to specify damping and strain rate dependant strength parameters to existing shear degradation failure criteria, enhancing model accuracy. The IEP material card is available as a user subroutine for Abaqus Explicit.